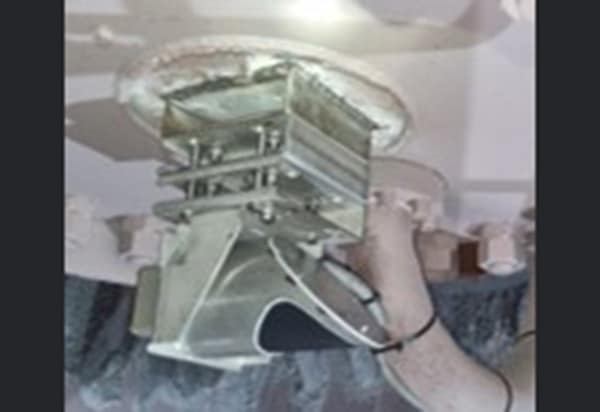
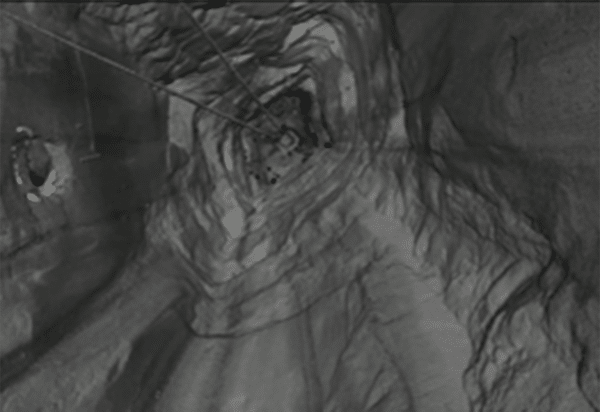
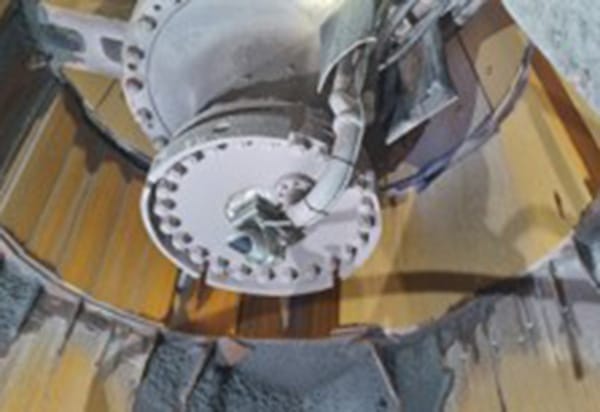
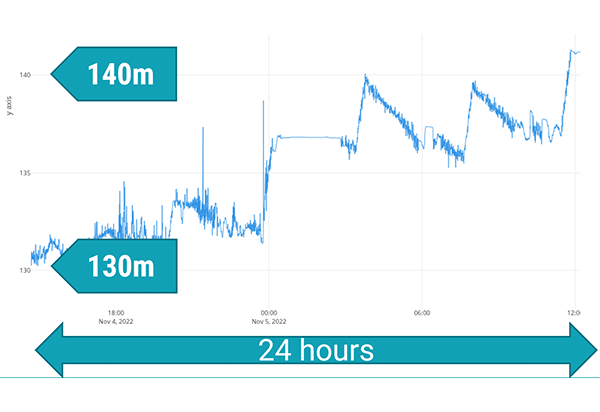
2D & 3D VAULT SCAN
Norway Orepass
A 1D iLDR-H radar sensor under a primary crusher measures the level of a 200 meter long ore pass in an iron ore mine in Norway. The system shows the continuous changes in the level, allowing the customer to control the crushing and conveying.
In addition, the information on ore pass volume and changes in the ore pass allows informed decisions to be made to ensure that the ore pass is not worn or blocked.