100% PERFORMANCE -
0% MAINTENANCE.
iLDR-C
1D compact dynamic radar for industrial applications
Product description
The iLDR sensor offers a remarkable measurement rate of 12,000 Hz, allowing for object detection at distances of up to 1000 meters. Designed to endure harsh environments, it provides reliable and accurate results even under demanding industrial conditions. With five available variants, the iLDR now caters to a wide range of applications beyond its original purpose, including use in steel production.
Application area
Our advanced iLDR solutions are ideal for operations requiring high precision and durability, even in the toughest environments. These sensors enhance efficiency and accuracy across diverse industrial sectors, including:
- Positioning in Shotcrete Machine Automation
- High-Precision Measurements in Steel Production
- Long-Distance Object Detection in Harsh Conditions
The iLDR sensor’s robust design and versatility make it a perfect choice for numerous industrial applications where reliability and precision are paramount.
Technical information
DATA SHEET
iLDR-C
SENSOR
1D compact dynamic radar
for industrial applications
MEASUREMENT RATE
TRANSMITTING FREQUENCY
122–123 GHz (ITU ISM band – in some countries limited to 122.25–123 GHz)
Max. range: 119–126 GHz (optional with site specific permit)
POWER SUPPLY
37–56 V DC
Ethernet: IEEE 802.3af/at Mode A (phantom power)
Exemplary supported PoE injectors: PLANET IPOE-171-95W, Moxa INJ-24A-T, Trendnet TI-PG541i
DIMENSIONS
Ø50 x 122 mm
WEIGHT
HOUSING
Anodized aluminium
INERTIAL SENSOR
Derived features
- Plant health monitoring
- Orientation validation
Specification
- Gyroscope sensitivity error: ±1%
- Gyroscope noise: ±4 mdps/√Hz
- Accelerometer noise: 100 µg/√Hz
- ±2000 dps integrated 16-bit ADCs
- Acceleration limit ±16g
- Industrial Range: -40°C to +85°C
Hazardous Locations (HazLoc)
CERTIFICATE
ZONES / GROUP
EPL (EQUIPMENT PROTECTION LEVEL)
Mb
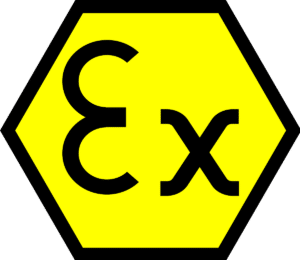
Standard Data Output
- Distance
- Angular Information
- Intensity
- Speed (using doppler principle)
- Target (if set up)
Sensor Interfaces:
- Colossus (according to ASRL - Autonomous Space Robotics Lab specification)
- Asterix CAT 240 (EUROCONTROL Specification for Surveillance Data Exchange)
- OPC UA (Open Platform Communications Unified Architecture)
- MQTT (MQ Telemetry Transport protocol for machine-to-machine communication)
- ROS2 (Robotic Operating System Version 2) standards, being downwards compatible to ROS1.
- SDK (Software Development Kit) for direct integration.
Sensor Networks:
- Our sensors are capable to be working in a sensor network together with other sensors of the same kind or mixed with other indurad sensors.
In addition to a direct TCP/IP connection via Gbit Ethernet, our integrated sensor network offers various interfaces (e.g., industrial interfaces like Profibus DP, Modbus TCP, dry contacts) and connection options (Starlink, 4G, 5G, etc.). Having executed projects in diverse industrial environments, from jungles to icy regions, indurad possesses the technology and expertise to provide comprehensive support.
iLDR-M
1D radar for short to medium-range applications
Product description
The iLDR sensor offers a remarkable measurement rate of 12,000 Hz, allowing for object detection at distances of up to 1000 meters. Designed to endure harsh environments, it provides reliable and accurate results even under demanding industrial conditions. With five available variants, the iLDR now caters to a wide range of applications beyond its original purpose, including use in steel production.
Application area
Our advanced iLDR solutions are ideal for operations requiring high precision and durability, even in the toughest environments. These sensors enhance efficiency and accuracy across diverse industrial sectors, including:
- Positioning in Shotcrete Machine Automation
- High-Precision Measurements in Steel Production
- Long-Distance Object Detection in Harsh Conditions
The iLDR sensor’s robust design and versatility make it a perfect choice for numerous industrial applications where reliability and precision are paramount.
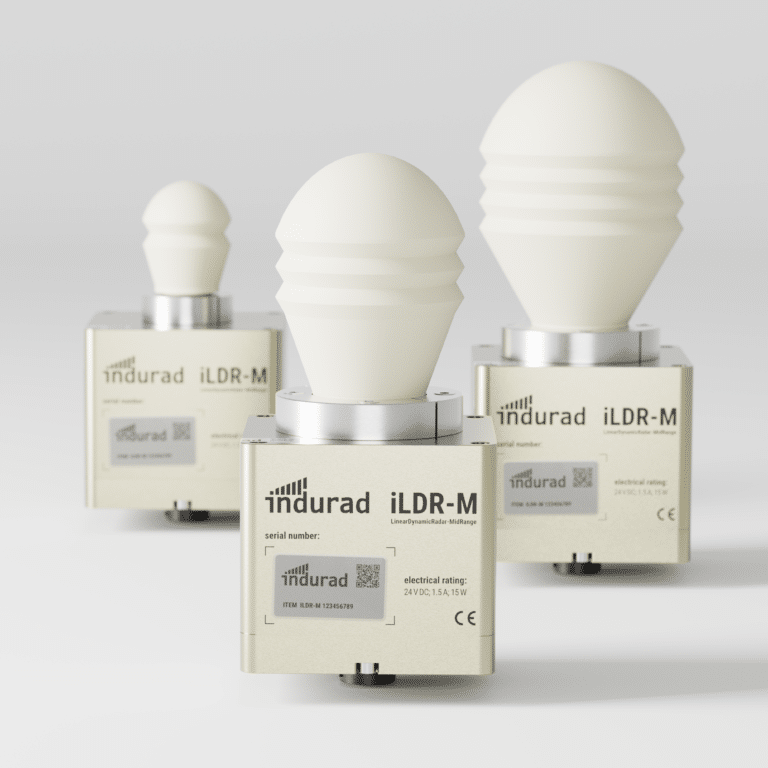
iLDR-M-DN050
iLDR-M-DN080
iLDR-M-DN100
Technical information
DATA SHEET
iLDR-M-DN100
SENSOR
MEASUREMENT RATE
Up to 12,000 Hz
TRANSMITTING FREQUENCY
76.020–76.980 GHz
77.020–80.930 GHz
71.500–84.000 GHz (on request)
POWER SUPPLY
DIMENSIONS
100 x 100 x 245 mm
WEIGHT
3.3 kg
HOUSING
INERTIAL SENSOR
Derived features
- Plant health monitoring
- Orientation validation
Specification
- Gyroscope sensitivity error: ±1%
- Gyroscope noise: ±4 mdps/√Hz
- Accelerometer noise: 100 µg/√Hz
- ±2000 dps integrated 16-bit ADCs
- Acceleration limit ±16g
- Industrial Range: -40°C to +85°C
Hazardous Locations (HazLoc) - only iLDR-H-DN100 (V3)
CERTIFICATE
ZONES / GROUP
EPL (EQUIPMENT PROTECTION LEVEL)
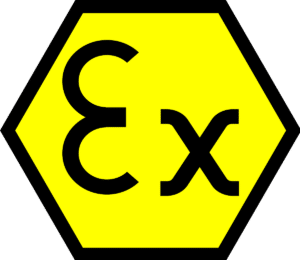
Standard Data Output
- Distance
- Angular Information
- Intensity
- Speed (using doppler principle)
- Target (if set up)
Sensor Interfaces:
- Colossus (according to ASRL - Autonomous Space Robotics Lab specification)
- Asterix CAT 240 (EUROCONTROL Specification for Surveillance Data Exchange)
- OPC UA (Open Platform Communications Unified Architecture)
- MQTT (MQ Telemetry Transport protocol for machine-to-machine communication)
- ROS2 (Robotic Operating System Version 2) standards, being downwards compatible to ROS1.
- SDK (Software Development Kit) for direct integration.
Sensor Networks:
- Our sensors are capable to be working in a sensor network together with other sensors of the same kind or mixed with other indurad sensors.
In addition to a direct TCP/IP connection via Gbit Ethernet, our integrated sensor network offers various interfaces (e.g., industrial interfaces like Profibus DP, Modbus TCP, dry contacts) and connection options (Starlink, 4G, 5G, etc.). Having executed projects in diverse industrial environments, from jungles to icy regions, indurad possesses the technology and expertise to provide comprehensive support.
iLDR-H
1D radar for high-range industrial applications
Product description
The iLDR sensor offers a remarkable measurement rate of 12,000 Hz, allowing for object detection at distances of up to 1000 meters. Designed to endure harsh environments, it provides reliable and accurate results even under demanding industrial conditions. With five available variants, the iLDR now caters to a wide range of applications beyond its original purpose, including use in steel production.
Application area
Our advanced iLDR solutions are ideal for operations requiring high precision and durability, even in the toughest environments. These sensors enhance efficiency and accuracy across diverse industrial sectors, including:
- Positioning in Shotcrete Machine Automation
- High-Precision Measurements in Steel Production
- Long-Distance Object Detection in Harsh Conditions
The iLDR sensor’s robust design and versatility make it a perfect choice for numerous industrial applications where reliability and precision are paramount.
Technical information
DATA SHEET
iLDR-C
SENSOR
1D compact dynamic radar
for industrial applications
MEASUREMENT RATE
TRANSMITTING FREQUENCY
122–123 GHz (ITU ISM band – in some countries limited to 122.25–123 GHz)
Max. range: 119–126 GHz (optional with site specific permit)
POWER SUPPLY
37–56 V DC
Ethernet: IEEE 802.3af/at Mode A (phantom power)
Exemplary supported PoE injectors: PLANET IPOE-171-95W, Moxa INJ-24A-T, Trendnet TI-PG541i
DIMENSIONS
Ø50 x 122 mm
WEIGHT
HOUSING
Anodized aluminium
INERTIAL SENSOR
Derived features
- Plant health monitoring
- Orientation validation
Specification
- Gyroscope sensitivity error: ±1%
- Gyroscope noise: ±4 mdps/√Hz
- Accelerometer noise: 100 µg/√Hz
- ±2000 dps integrated 16-bit ADCs
- Acceleration limit ±16g
- Industrial Range: -40°C to +85°C
Hazardous Locations (HazLoc)
CERTIFICATE
ZONES / GROUP
EPL (EQUIPMENT PROTECTION LEVEL)
Mb
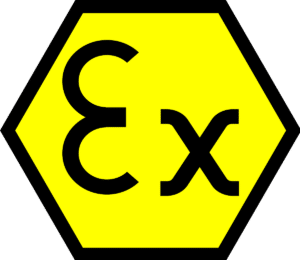
Standard Data Output
- Distance
- Angular Information
- Intensity
- Speed (using doppler principle)
- Target (if set up)
Sensor Interfaces:
- Colossus (according to ASRL - Autonomous Space Robotics Lab specification)
- Asterix CAT 240 (EUROCONTROL Specification for Surveillance Data Exchange)
- OPC UA (Open Platform Communications Unified Architecture)
- MQTT (MQ Telemetry Transport protocol for machine-to-machine communication)
- ROS2 (Robotic Operating System Version 2) standards, being downwards compatible to ROS1.
- SDK (Software Development Kit) for direct integration.
Sensor Networks:
- Our sensors are capable to be working in a sensor network together with other sensors of the same kind or mixed with other indurad sensors.
In addition to a direct TCP/IP connection via Gbit Ethernet, our integrated sensor network offers various interfaces (e.g., industrial interfaces like Profibus DP, Modbus TCP, dry contacts) and connection options (Starlink, 4G, 5G, etc.). Having executed projects in diverse industrial environments, from jungles to icy regions, indurad possesses the technology and expertise to provide comprehensive support.
100% PERFORMANCE - 0% MAINTENANCE.
100% PERFORMANCE - 0% MAINTENANCE.
MADE FOR HARSH CONDITIONS.
MADE FOR HARSH CONDITIONS.
INDURAD – INDUSTRIAL RADAR
Back in 2008, we invented the first 2D radar for industrial applications, the iconic iDRR (indurad DualRangeRadar). Since then, our design and manufacturing capabilities have continued to evolve – as have our sensors. Today, we are proud to offer a complete portfolio of unique radar sensors that help our customers achieve their productivity and sustainability goals every day, in all environmental conditions.
On the left-hand side, the illustration demonstrates the propagation of a radar wave around a dust particle measuring 3mm in diameter. This phenomenon exemplifies the radar’s efficacy as a covert mechanism for penetrating and visualizing through challenging environmental conditions such as dust, fog, snow, and steam.
Our extensive product portfolio is further enhanced by the inclusion of RTLS (Real-Time Location System) sensors, GNSS (Global Navigation Satellite System) sensors, and processing units.
While the majority of our sensors find primary applications within our own systems, we extend our services to original equipment manufacturers (OEMs) by providing ROS2 interface options.